Concrete is a widely used construction material worldwide, typically composed of Portland cement, aggregates (such as sand, gravel, or crushed stone) and water. Despite its strength and durability, traditional concrete has some limitations, including its high brittleness and heavyweight, which can lead to low tensile stress, strain, and cracking during the hardening stages. However, concrete can be reinforced with materials like steel to enhance its tensile strength, making it suitable for various construction applications [1].
The increasing use of plastics in many civil or industrial aspects has generated the availability of large quantities of non-biodegradable waste. The non-biodegradable nature of most plastics necessitates large storage spaces for plastic waste [2]. Yearly, plastic waste represents around 11% of the solid waste materials assembled [3]. Despite this, the characteristics of plastic, such as its relatively high durability, low weight, and low cost, made it impossible to dispense with plastic in the short term and opened the door to investment in plastic waste management and recycling [4].
Plastic waste has become a significant environmental problem in many aspects, such as its influence on aquatic life Click or tap here to enter text.[5]–[6] Click or tap here to enter text.. Many recent studies have given great hope to using plastic waste in construction applications, such as building mixtures [7]. However, the studies indicated challenges in recycling due to the organic and inorganic components of the waste plastic materials [8]. Using plastic waste as a raw material in concrete is considered a promising solution [9]. This solution can be accomplished by grinding the plastic waste into a fine powder or mixing it in large granules of different sizes [10]. This technique not only assists in decreasing plastic waste but also makes a sustainable construction material.
Concrete production is known to have a significant environmental impact due to its high consumption of natural resources, particularly sand and gravel, and its high carbon footprint from cement production [11]. Therefore, finding alternative materials with low costs and environmental impact is essential. Plastic waste, which is considered one of the most significant non-degradable solid pollutants, has the potential to be a sustainable alternative to traditional concrete materials.
Traditional concrete typically contains 12% cement, 80% sand, and gravel, which requires significant natural resources [12]. Using this mixture to produce bricks and concrete blocks results in products with great weight, making them unsuitable for many applications. Moreover, the widespread use of plastic materials in manufacturing, packaging, and consumer goods has led to a surge in plastic waste generation. Non-biodegradable plastic waste is one of the largest solid pollutants in the world's rivers, lakes, and oceans [13], [14].
The use of sustainable manufacturing processes, which includes non-traditional methods, recycling, and waste reuse to produce new materials, is becoming increasingly popular. Recently, there has been a growing emphasis on non-traditional brick production methods, particularly industrial waste, or waste recycling, aligning with sustainability goals. Several studies have appeared that explore the production of bricks using these creative approaches. One promising alternative material is plastic waste, considered one of the most significant solid non-degradable pollutants [15]. Polyethylene (PE) recycling is essential in diminishing environmental impact, conserving resources, and encouraging a circular economy by transforming used polyethene products into valuable raw materials to produce new items such as construction and automotive [16].
Researchers have studied the reuse of plastic waste in road construction, investigating its potential as a substitute for aggregates or as fillers in asphalt mixtures to promote sustainability [17], [18]. Moreover, plastic waste can be effectively employed in the production of cementitious composites by mixing it with other waste materials like recycled concrete, rice husk ash, fly ash, and silica fume, resulting in high stability and hardness, thereby specifying them as appropriate raw materials for cementitious composites [19]. In the production of cementitious composites, a various range of plastics, including resins (such as epoxy and polyester), polylactic acid (PLA), PVC, polystyrene, polyethylene terephthalate, HDPE, polypropylene, and LDPE, are employed [20]. Combining plastic waste powder or pellets with wood flour or cellulose fiber constructs a thermoformable wood-plastic matrix, producing eco-friendly doors [21]. Considerable studies have consistently emphasised the pivotal role of market demand as a critical driver in industrial applications where recycled materials can substantially contribute [22].
Nura Diana et al [23] investigated the use of plastic bottle waste as a substitute for fine aggregate in concrete production. Different gradations of plastic bottle waste (0%, 5%, 10%, and 12%) were tested, and the compressive strength of each variation was analyzed using regression and classical assumption tests. The results showed that the compressive strength decreased as the percentage of plastic waste increased, with the maximum strength achieved at 0% and 5% substitution (19.192 MPa and 16.414 MPa, respectively).
Zoe Harmonie Lee et al [24] investigated the use of chemically treated polyethylene terephthalate (PET) plastic waste as a substitute for natural aggregates in concrete to reduce plastic waste disposal. The study focused on the effects of hydrogen peroxide (H2O2) and calcium hypochlorite (Ca(ClO)2) treatments on PET plastic aggregates before incorporation in concrete. Concrete samples with 10%, 20%, and 30% replacement of natural aggregates with treated plastic aggregates were analyzed for physical and mechanical properties. Results showed that chemically treated plastic aggregates had no significant effect on fresh density but decreased the slump due to the roughened surface. The bond strength between the cementitious matrix and plastic aggregates improved.
Polystyrene waste was used as an alternative to sand and gravel to produce lightweight bricks. The results showed that the best percentage for manufacturing was 10% of polystyrene waste with the cement mixture [4]. Polyethene waste has also been used with the concrete mixture in proportions ranging from 10-50%. Experiments showed that workability increases with an increase in the percentage of plastic waste up to 50% before decreasing. Additionally, the density of the concrete mixture decreases gradually with an increase in the proportion of plastic in the mixture [9]. Similarly, polypropylene (PP) waste was used as a substitute for sand in the concrete mixture, but the results showed weak bonding and cohesion between cement and plastic waste [8]. Polyvinyl chloride residues and plastic bags have also been used with the concrete mixture to produce blocks for street sidewalks [10], [25].
Earlier studies have mainly focused on generally incorporating plastic waste into concrete. In contrast, the current research specifically examines incorporating circular cross-sections of polyethylene and polypropylene waste cut into small lengths to create a novel composition with Portland cement. Instead of using sand and gravel, circular cross sections of polyethylene and polypropylene waste, cut into small lengths less than 5 mm, were mixed to attain the preferred composition with Portland cement. This method eliminates the need for sand and gravel and does not require heat. The resulting mixture can be formed with or without pressing and has the potential to reduce costs and pollutants associated with traditional concrete production significantly.
The experimental work gives a new procedure for utilising plastic waste with cement in the construction industry. This approach eliminates the demand for sand and gravel in the concrete mixture and does not need a heating or melting process for the plastic waste. The resultant mixture can be constructed with or without pressing, making it cost-effective and sustainable. The collected polyethylene and polypropylene waste were isolated and cut into small pellets. The plastic waste was washed to remove any suspended materials.
Several variables affect how much water is needed for washing, including the type and condition of the plastic waste. Enough water is used to thoroughly rinse and remove impurities or contaminants from the plastic waste. The washed waste materials then added to a melting and extrusion machine to produce a continuous circular section resembling wire. The diameter of the wire was 3 mm, and the length was 2 meters. The resulting wires were then cut into small plastic pellets of dimensions of length x diameter of 3x3 mm, 3.5x3 mm, and 4x3 mm, as shown in Figure 1. The Chemical composition and Mechanical properties of Polyethylene and Polypropylene are indicated in Table 1 and Table 2 respectively.
Polyethylene and polypropylene waste pellets after processing and cutting
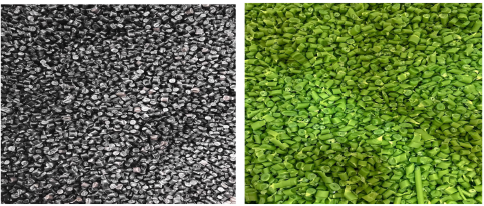
Chemical composition of Polyethylene and Polypropylene pellets
Chemical Component | Polyethylene (PE) | Polypropylene (PP) |
---|---|---|
Carbon | 85.0 - 97.5% | 85.0 - 87.5% |
Hydrogen | 12.5 - 14.5% | 12.5 - 14.5% |
Other | 0 - 2.5% | 0 - 2.5% |
Mechanical properties of Polyethylene and Polypropylene pellets
Mechanical Property | Polyethylene (PE) | Polypropylene (PP) |
---|---|---|
Tensile strength | 10 - 40 MPa | 30 - 50 MPa |
Elongation at break | 100 - 800% | 200 - 600% |
Flexural modulus | 0.1 - 1.5 GPa | 1.5 - 2.5 GPa |
Impact strength | 5 - 25 kJ/m2 | 30 - 50 kJ/m2 |
Compressive strength | 2 - 15 MPa | 10 - 25 MPa |
Melting temperature | 110 - 135°C | 130 - 170°C |
According to the mixing ratios in Table 3, the raw materials were mixed to prepare them for brick production. The volumetric material quantities used in the mixture were 1.5 and 2.5 for Portland cement and either polyethylene or polypropylene, respectively, besides the 0.5 of water. So, the mixture percentages were 33% allocated for polyethylene or polypropylene, 56% for Portland cement, and 11% for water. Figure 2 illustrates the preparation of raw plastic bricks material where the mixing process was done manually until the homogeneous mixture was reachedIt is worth mentioning that the polyethylene and polypropylene pellets mixtures were prepared individually to ensure they were accurately weighed and proportioned. The detailed preparation of raw materials ensured that the resulting bricks would have a uniform composition and mechanical properties.
Plastic brick preparation raw materials mixing ratios
Materials | Volumetric quantity | Mixture % |
---|---|---|
Portland cement | 2.5 | 56 |
Polyethylene or polypropylene pellets | 1.5 | 33 |
water | 0.5 | 11 |
Prepare and mix polyethylene or polypropylene waste pellets with Portland cement
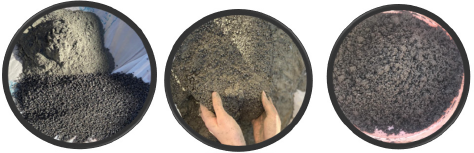
The production process of plastic reinforced bricks begins with the preparation of the mixture by weighing the raw materials according to the quantities shown in Table 2. The mixture is then manually mixed with water until homogeneous, with separate mixtures of polyethylene and polypropylene waste depending on the plastics pellet's dimensions of length and diameter "of 3x3 mm, 3.5x3 mm, 4x3 mm". Figure 3 indicates the semi-automated machine that produced plastic-reinforced bricks; the brick construction mold dimensions were 23x11x7 cm. This process ensures that the plastic waste is uniformly distributed in the brick, resulting in a consistent product.
Pressing of polyethylene or polypropylene waste with cement mixture
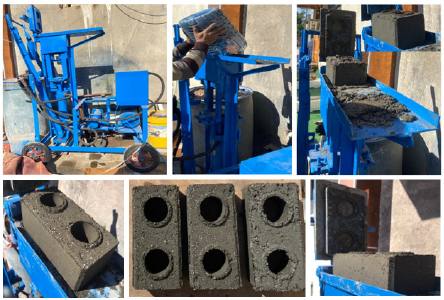
Production of plastic-reinforced bricks continues after the pressing process, and then, the wet brick must be dried in the air to minimize the moisture content. The drying process is also necessary to ensure that the resulting plastic bricks do not crack or deform during curing. Once dry, the plastic bricks are dipped in water for seven days. Curing allows the bricks to adhere well and reach the preferred compression strength. Figure 4 displays the bricks being dipped in water during the curing process.
Plastic blocks in water dipping
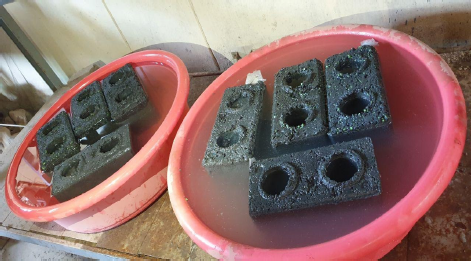
The current study focuses on manufacturing building bricks by adding polyethylene or polypropylene waste granules as an alternative to the gravel used in traditional bricks. The study discusses the possibilities of production through three important aspects:
The general appearance of the plastic-reinforced bricks and the possibility of lining them together.
Measuring the weights of the resulting bricks.
The extent to which the plastic-reinforced bricks bear the loads is studied by measuring the compressive strength and the nature of the failure or shattering that occurs after compression.
The appearance of plastic reinforced bricks is a crucial factor in determining their usability as a sustainable construction material. The results of the study showed that there was no scattering or fragmentation in the bricks reinforced with recycled plastic as shown in Figure 5. The results show that the production strategy used in this study successfully produces robust and long-lasting bricks.
Plastic reinforced bricks Samples produced by using plastic waste
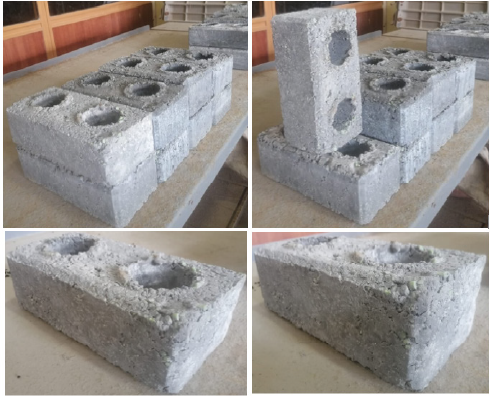
Furthermore, paving the bricks on each other was also successful, as the plastic bricks in the lower rows were not affected by loading additional bricks, making it look like a conventional brick to the user. This is a promising result as it indicates that the plastic-reinforced bricks can be used in a similar way as traditional bricks without compromising their structural integrity.
It should be noted here that the manufactured models contained two separate cavities, each 4 cm in diameter, on the width of the brick in order to reduce the weight as well as the use of binders when building. Despite these cavities, the general appearance of the resulting bricks has not been affected, and it is an additional support point.
This production method eliminates the need for sand and gravel, and no heat is required. Additionally, using plastic waste as a substitute for traditional concrete materials creates a sustainable and cost-effective construction material that helps mitigate plastic waste pollution. The tests indicate the possibility of plastic-reinforced bricks as an environmentally friendly alternative to conventional bricks.
After the production process of the plastic-reinforced bricks, an accurate scale is used to measure the weight of the resulting bricks to compare them with traditional cement bricks. Several randomized samples were used to measure weight. The weights ranged between 2.74 and 2.91 kg, less than traditional cement bricks' standard weight of 3.65 kg. It should be noted here that the plastic pullets' diameter is 3 cm, while their lengths range between 3 and 4 cm. The main reason for the lower weight of plastic reinforced bricks is the use of plastic waste as a partial replacement for cement, which has a lower density compared to cement, resulting in a decrease in the overall weight of the brick [26].
The plastic brick dimension is 23x11x7 cm. There is a small difference in weight between the bricks produced using pellets of PE and PP, as the average weight of the plastic bricks made were 2.83 kg and 2.81 PE and PP, respectively, as shown in Table 4.
Plastic pellets dimensions in bricks specimens sets
# | Bricks materials | Pellet length [cm] | Pellet diameter [cm] | Weight [kg] | Compression Strength [N/cm2] |
---|---|---|---|---|---|
1 | Bricks reinforced with PP pellets | 3 | 3 | 2.74 | 754 |
2 | Bricks reinforced with PP pellets | 3.5 | 3 | 2.85 | 746 |
3 | Bricks reinforced with PP pellets | 4 | 3 | 2.85 | 711 |
4 | Bricks reinforced with PP pellets | Ran | 3 | 2.89 | 789 |
5 | Bricks reinforced with PE pellets | 3 | 3 | 2.75 | 655 |
6 | Bricks reinforced with PE pellets | 3.5 | 3 | 2.87 | 539 |
7 | Bricks reinforced with PE pellets | 4 | 3 | 2.88 | 521 |
8 | Bricks reinforced with PE pellets | Ran | 3 | 2.91 | 698 |
9 | Cement bricks | - | - | 3.65 | 1145 |
The difference in physical properties can play an important role in the difference in weights between bricks reinforced with waste polypropylene pellets and those reinforced with waste polyethylene pellets. For example, the density of polyethylene is slightly higher than the density of polypropylene. On the other hand, the weight of the plastic-reinforced brick can be affected by the shape and size of the plastic material pellets that make it up. The positive point here is that the slight difference in the weights of the bricks reinforced with plastic waste, whether PE or PP waste, did not affect the performance of the bricks' strength in the compression tests.
When comparing traditional cement bricks with those produced by adding elements from PP and PE waste instead of gravel, the difference in weight was a decisive factor in the comparison. The weights of bricks reinforced with plastic waste showed an impressive decrease in weight, about 20% less than the conventional cement bricks, and this matter is considered a catalyst for more research related to sustainability and waste management issues. The resulting weight reduction of 20% is quite reasonable, of 4% is related to investigations such as Tafheem et al. [27].
The weight decrease observed in the bricks produced using recycled PE and PP compared to conventional cement bricks can have several advantages for the building industry, such as decreasing transportation costs, making the bricks easier to handle and install, and needing less production power. Additionally, using recycled plastic in building materials can positively impact the environment by reducing plastic waste [28]. Employing recycled plastic in buildings can reduce the extraction of natural resources such as sand, gravel, and clay, often used in conventional cement bricks [29]. Besides, it is considered a sustainable alternative to conventional concrete materials that are cost-effective and can support mitigating plastic waste pollution.
Compression strength test is a type of mechanical test that measures the ability of a material to resist compression or crushing. It is commonly used to determine the strength and durability of materials such as concrete, bricks, and metals [30]. The test involves applying a compressive load to a specimen until it fails or is crushed. The compressive strength of the material is then calculated by dividing the maximum load applied during the test by the cross-sectional area of the specimen. In the case of plastic reinforced bricks, compression strength tests are used to evaluate the strength and durability of the bricks made from recycled plastic. The test involves preparing a sample of the plastic reinforced bricks according to a standard ASTM C67 procedure and subjecting it to a compressive load using a hydraulic testing machine. The maximum load that the sample can withstand before failing is recorded, and the compression strength of the brick is calculated using the cross-sectional area of the sample. A universal compression machine used to measuring the compression strength of all specimens as indicated in Figure 6 where Figure 6a represents the compression test machine, Figure 6b represents PP reinforced brick before test, while Figure 6c-e represent bricks after test for PP reinforced brick, PE reinforced bricks, and traditional cement brick respectively.
Compression test a) compression test machine, b) PP reinforced brick before test, c) PP reinforced brick, d) PE reinforced bricks, e) Traditional cement brick
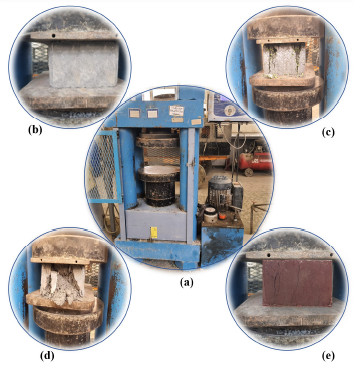
Based on the Table 4, it can be observed that the compression strength of the plastic reinforced bricks produced from polypropylene (PP) ranges from 711-754 N/cm2. Meanwhile, the compression strength of the plastic reinforced bricks produced from polyethylene (PE) ranges from 521-655 N/cm2. It is interesting to note that the compression strength of the traditional cement bricks is significantly higher, with a value of 1145 N/cm2. Overall, the results suggest that while plastic reinforced bricks can be produced using recycled materials such as PP and PE, their compression strength may not be as high as traditional cement bricks. Considering the decreased compression strength observed in plastic-reinforced bricks compared to traditional cement bricks, evaluating their suitability for specific applications is essential. While plastic-reinforced bricks may not be qualified for high-load-bearing applications demanding extremely high compression strength, they can still be a feasible choice for different non-load-bearing or lightweight construction objectives. These contain partition walls or decorative components. The advantages of plastic-reinforced bricks, such as their reduced weight, the potential for a plastic waste deduction, and cost-effectiveness, make them particularly appropriate for applications where weight reduction and sustainability considerations are prioritized.
The divergence in compression strength between plastic-reinforced bricks created from polypropylene (PP) and polyethylene (PE) can be attributed to several aspects related to the material characteristics of PP and PE, such as strength and stiffness, where polypropylene typically exhibits higher strength and stiffness corresponded to polyethylene. This effect can enhance deformation resistance, resulting in higher compression bricks. Furthermore, the interfacial bonding between the plastic particles and the cement matrix plays a crucial role in determining the overall strength of the plastic-reinforced bricks. The interfacial bonding is more powerful in PP-reinforced bricks than in PE-reinforced bricks. However, further experimentation and optimization of the production process may yield better results. The need for additional experimentation derives from the complexity of the manufacturing process and the significant variables concerned. Researchers can refine the mixture ratios, pellet dimensions, and other parameters. Furthermore, further studies can help identify the most suitable plastic waste types and additives to improve the mechanical properties of bricks.
Looking at the results for the different experimental sets of plastic reinforced bricks made with PP and PE, observations demonstrate variations in the compression strength attributed to the length and diameter of the plastic pellets utilised in the study. In the case of the PP bricks, a noticeable trend is observed where the compression strength tends to decline as the length of the pellets grows. The bricks produced with the smallest pellets (3x3 mm) have the most increased compression strength (754 N/cm2), while the bricks produced with the largest pellets (4x3 mm) have the lowest compression strength (711 N/cm2). This tendency aligns with expectations, as smaller pellets can pack more tightly together, resulting in a stronger and more compact structure. Likewise, in the case of the PE bricks, a similar trend is evident, although the impact of length could be more noticeable.
As shown in Table 4 can be the compression strength. The plastic waste pellets are cut into three sizes: (3 x 3 mm), (3 x 3 mm), and (4 x 3 mm). The PP brick tests showed that the compression strength is inversely proportional to the size of the pellets, as the smaller pellets (3 x 3 mm) gave better performance, reaching 754 N/cm2 compression strength against 711 N/cm2 for bricks reinforced with larger plastic waste pellets. Concerning the bricks reinforced with PE waste, the matter was similar, except that the compression strength was less than that obtained using PP waste pellets. As it was previously shown that the raw material preparation processes could include heating and boiling, the fact that the melting point of PP is greater than that of PE may have contributed to its greater compression strength and higher hardness, and this is consistent with many previous studies related to the use of PP and PE in industrial applications [31], [32]. To find out the possibility of using a mixture of waste pellets of different sizes in manufacturing bricks, the results were unexpected, as the resulting bricks gave higher compressive strength than those obtained from using the waste of one size. The pellets could be of different sizes, allowing for a better distribution within the cement mixture, which led to more cohesive and homogeneous plastic bricks. As a result, the properties of each type of plastic waste significantly impact the compression strength and performance of the bricks reinforced with plastic waste.
Figure 7a-c represents the failure profiles of PP-reinforced, PE-reinforced, and conventional cementitious bricks. The possible reasons for the failure of the samples of bricks reinforced with plastic waste may not differ much from the reasons studied for the difference in compressive strength.
The length of the waste pellets was a critical factor in the failure of the models, as the longer the length of the PP or PE waste pellets, the larger the failure and the more shattered the appearance of the resulting bricks after the test. As the length of the pellets increases, empty spaces or gaps are generated inside that may increase the porosity or the possibility of absorbing larger quantities of water than required during the manufacturing period. Accordingly, the resulting plastic bricks will be less durable, and the possibility of breaking or disintegrating them will be higher.
The direction of the PP or PE waste pellets may also be influential, where the irregular distribution of the waste components of the resulting plastic-reinforced bricks leads to weak areas with a high-stress concentration. The stress concentration leads to the failure and shattering of the resulting plastic bricks. Further future studies can lead to finding the optimal size of PP or PE waste pellets and establishing the optimal size distribution.
Brick failure shapes a) PP reinforced brick, b) PE reinforced brick, c) cement brick
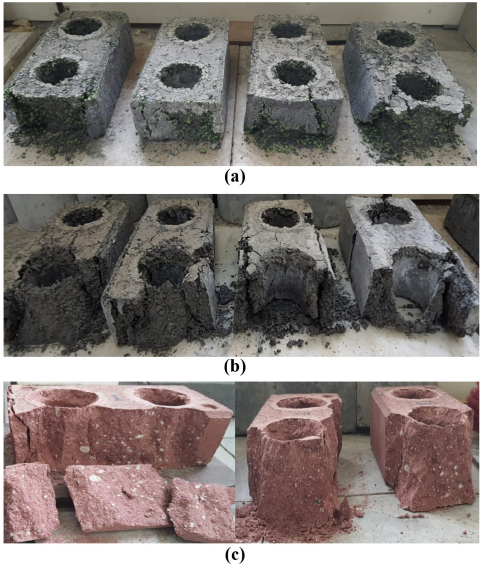
the results of this study suggest that plastic reinforced bricks have the potential to be a sustainable and environmentally friendly alternative to traditional concrete materials. Further experimentation and optimization of the production process can lead to even better results, paving the way for more widespread adoption of this technology in the construction industry. There are several conclusions from this study can be summarized below:
Utilizing recycled plastic waste as a partial replacement for cement in producing plastic-reinforced bricks presents a sustainable and eco-friendly solution that decreases plastic waste pollution.
The appearance of the plastic reinforced bricks produced in this study was durable and sturdy, with no fragmentation or scattering observed. Additionally, the bricks can be paved on each other in a similar way to traditional bricks without compromising their structural integrity.
The weight of plastic reinforced bricks produced from polypropylene (PP) and polyethylene (PE) ranged from 2.74-2.91 kg, which is around 20% less than traditional cement bricks. This weight reduction can lead to several benefits such as reducing transportation costs, making the bricks easier to handle and install, and requiring less energy to manufacture.
The compression strength of the plastic reinforced bricks ranged from 521-754 N/cm2, which is lower than that of traditional cement bricks. However, optimizing the size and shape of the plastic pellets used in the mixture can result in even stronger and more durable composite bricks.
The high compression strength and good appearance of the PRT brick, combined with the possibility of paving, indicate that this type of brick can provide structural integrity under various loading conditions.
The failure and damaging appearance of plastic reinforced bricks can be affected by several factors, with length being one of the most important ones. The length and shape of the plastic pellets used should be optimized to improve the overall quality and reduce the likelihood of failure.
Finally, the reduction in compression strength of plastic-reinforced bricks compared to conventional bricks has importance for their suitability in construction. It is essential to conduct further research and testing to ensure that the plastic-reinforced bricks satisfy the required construction standards and withstand real-world structural needs. Failure of reinforced bricks can compromise safety and structural integrity and pose probable hazards, highlighting the significance of detailed testing and adherence to construction standards.
Use of plastic aggregates in concrete ,International Journal of Innovative Technology and Exploring Engineering , Vol. 9 (1),pp 44064412 , 2019, https://doi.org/https://doi.org/10.35940/ijitee.A5088.119119
, Lightweight foamed concrete as a promising avenue for incorporating waste materials: A review ,Resources, Conservation and Recycling , Vol. 164 ,pp 105103 , 2021, https://doi.org/https://doi.org/10.1016/j.resconrec.2020.105103
, Recycling of Polyethylene Waste to Produce Plastic Cement ,Procedia Manuf , Vol. 8 ,pp 635642 , 2017, https://doi.org/https://doi.org/10.1016/j.promfg.2017.02.081
, , Proceedings of Civil and Water Resources Engineering Conference, 3-4 November 2017 , 2017
, Sustainable Manufacturing Process Applied to Produce Waste Polymer-Polymer Matrix Composites ,Environmental Research, Engineering and Management , Vol. 79 (1),pp 122132 , 2023, https://doi.org/https://doi.org/10.5755/j01.erem.79.1.32907
, Confronting plastic pollution to protect environmental and public health ,PLoS Biology , Vol. 19 (3),pp e3001131 , 2021, https://doi.org/https://doi.org/10.1371/JOURNAL.PBIO.3001131
, , Effect of Microplastic on the Human Health , 2023, https://doi.org/https://doi.org/10.5772/intechopen.107149
, The Influence of Nano-SiO2 and Recycled Polypropylene Plastic Content on Physical, Mechanical, and Shrinkage Properties of Mortar ,Advances in Civil Engineering , Vol. 2019 ,pp 6960216 , 2019, https://doi.org/https://doi.org/10.1155/2019/6960216
, Engineering properties of concrete with waste recycled plastic: A review ,Sustainability (Switzerland) , Vol. 10 (11),pp 3875 , 2018, https://doi.org/https://doi.org/10.3390/su10113875
, Study the effect of plastic waste on strength of concrete ,International Journal of Advance Research and Development , Vol. 3 (7),pp 3639 , 2018
, Environmental impacts and decarbonization strategies in the cement and concrete industries ,Nat Rev Earth Environ , Vol. 1 (11),pp 559573 , 2020, https://doi.org/https://doi.org/10.1038/s43017-020-0093-3
, Some properties of sustainable concrete with mixed plastic waste aggregate ,IOP Conference Series: Materials Science and Engineering , Vol. 737 ,pp 012073 , 2020, https://doi.org/https://doi.org/10.1088/1757-899X/737/1/012073
, Plastic waste: Challenges and opportunities ,Waste Management and Research , Vol. 39 (5),pp 629630 , 2021, https://doi.org/https://doi.org/10.1177/0734242X211013428
, The plastic waste problem in Malaysia: management, recycling and disposal of local and global plastic waste ,SN Applied Sciences , Vol. 3 (4),pp 437 , 2021, https://doi.org/https://doi.org/10.1007/s42452-021-04234-y
, An evaluation of marine sediments in terms of their usability in the brick industry: Case study port of Koper ,Journal of Sustainable Development of Energy, Water and Environment Systems , Vol. 6 (1),pp 7888 , 2018, https://doi.org/https://doi.org/10.13044/j.sdewes.d5.0183
, Low-Density Polyethylene Plastic Waste to Liquid Fuel Using Pyrolysis Method: an Effect of Temperatures on the Oil Yields Physicochemical Properties ,Journal of Sustainable Development of Energy, Water and Environment Systems , Vol. 10 (3),pp 1090402 , 2022, https://doi.org/https://doi.org/10.13044/j.sdewes.d9.0402
, Plastic wastes to construction products: Status, limitations and future perspective ,Case Studies in Construction Materials , Vol. 12 ,pp e00330 , 2020, https://doi.org/https://doi.org/10.1016/j.cscm.2020.e00330
, Sustainable use of recycled waste glass as an alternative material for building construction - A review ,IOP Conference Series: Materials Science and Engineering , 2019, https://doi.org/https://doi.org/10.1088/1757-899X/640/1/012073
, Recycling plastic waste materials for building and construction Materials: A minireview ,Mater Today Proc , Vol. 62 (640),pp 012073 , 2022, https://doi.org/https://doi.org/10.1016/j.matpr.2022.04.226
, Use of recycled plastic in concrete: A review ,Waste Management , Vol. 28 (10),pp 18351852 , 2008, https://doi.org/https://doi.org/10.1016/j.wasman.2007.09.011
, Use of recycled plastics in wood plastic composites - A review ,Waste Management , Vol. 33 (9),pp 18981905 , 2013, https://doi.org/https://doi.org/10.1016/j.wasman.2013.05.017
, Converting waste plastics into construction applications: A business perspective ,Environ Impact Assess Rev , Vol. 96 ,pp 106814 , 2022, https://doi.org/https://doi.org/10.1016/j.eiar.2022.106814
, An Experimental Study of Plastic Waste as Fine Aggregate Substitute for Environmentally Friendly Concrete ,Advances in Technology Innovation , Vol. 6 (3),pp 179190 , 2021, https://doi.org/https://doi.org/10.46604/aiti.2021.6930
, Modification of Waste Aggregate PET for Improving the Concrete Properties ,Advances in Civil Engineering , Vol. 2019 ,pp 6942052 , 2019, https://doi.org/https://doi.org/10.1155/2019/6942052
, Plastic Wastes as a Raw Material in the Concrete Mix: An Alternative Approach to Manage Plastic Wastes in Developing Countries ,Int J Waste Resour , Vol. 10 (3), 2020, https://doi.org/https://doi.org/10.35248/2252-5211.20.10.382
, Producing sustainable concrete with plastic waste: A review ,Environmental Challenges , Vol. 9 ,pp 100626 , 2022, https://doi.org/https://doi.org/10.1016/j.envc.2022.100626
, Experimental investigation on the properties of concrete containing post-consumer plastic waste as coarse aggregate replacement ,Journal of Materials and Engineering Structures , Vol. 5 ,pp 2331 , 2018
, Utilisation of plastic waste as aggregate in construction materials: A review ,Construction and Building Materials , Vol. 296 ,pp 123669 , 2021, https://doi.org/https://doi.org/10.1016/j.conbuildmat.2021.123669
, The role of new material technologies for sustainable practice in the concrete industry ,PICMET: Portland International Center for Management of Engineering and Technology, Proceedings ,pp 17381744 , 2009, https://doi.org/https://doi.org/10.1109/PICMET.2009.5261972
, Porous concrete pavement containing nanosilica from black rice husk ash ,New Materials in Civil Engineering ,pp 493527 , 2020, https://doi.org/https://doi.org/10.1016/B978-0-12-818961-0.00014-4
, Effect of crystallinity of polyethylene with different densities on breakdown strength and conductance property ,Materials , Vol. 12 (11),pp 1746 , 2019, https://doi.org/https://doi.org/10.3390/ma12111746
, Molecular structure, crystallinity and morphology of polyethylene/ polypropylene blends studied by Raman mapping, scanning electron microscopy, wide angle X-ray diffraction, and differential scanning calorimetry ,Polym J , Vol. 38 (11),pp 11271136 , 2006, https://doi.org/https://doi.org/10.1295/polymj.PJ2006056
,